We Work Smarter
At Harrison Steel, we leverage the latest technology to get a better end product. Sophisticated engineering software, tightly-controlled manufacturing processes, unrivaled quality programs, and a motivated, non-union workforce are the not-so secret ingredients to our top-quality castings. Our U.S. plant in Attica, IN is capable of producing castings netting from 400 to 18,000 pounds and stretches out over 700,000 square feet—all driven by the industry’s latest technology.
Advanced Technology | Increased In-House Capabilities | Improved Value Stream
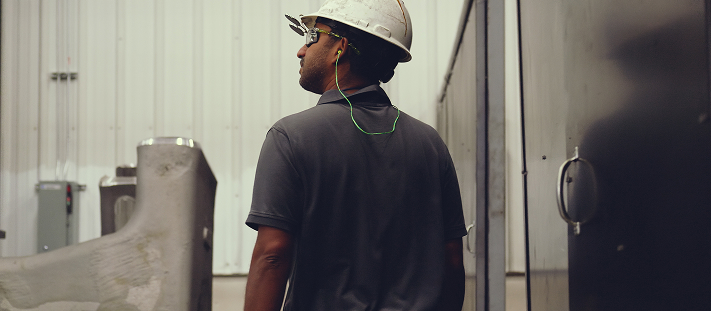
Finish Options
We offer both rough and finish machining for our global customers, providing options on how cast parts are finished prior to delivery. Our new Finish Machine Shop features the Mazak V100 and E1850 machines. This recent expansion drives up our capabilities to offer turnkey solutions and provide significant savings for customers.
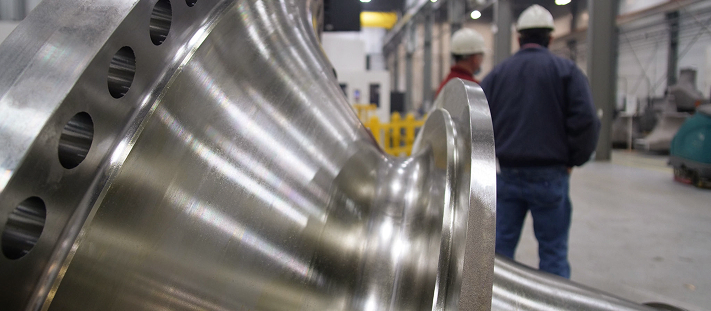
Material Options
Our material capabilities run the gamut from carbon to low and medium alloy steels, pressure vessels, high strength, and special purpose. Plus, we can produce any specific customer grades on request.
“The management team at Harrison Steel has been very proactive to ensure that HS remains globally competitive. Their commitments to 5S, the initiative to make their quality systems more robust and the significant upgrade to their value add capabilities have been very impressive. In my opinion, HS is positioned to be an industry leader for many years to come.”
– Casting Buyer, Energy Industry